Theme: Knowledge exchange
Authors: Dr Tom Allen (Manchester Metropolitan University), Prof Andy Alderson (Sheffield Hallam University) and Dr Stefan Mohr (HEAD)
Keywords: Sport, Tennis, Material, Auxetic, Mechanics
Abstract: The case study is interesting as it combines the engaging topics of smart materials and sports engineering, and showcases the release of a sports product. The work is underpinned by academic papers, include a teaching focus one detailing how materials have influenced tennis rackets dating back to the origins of the game. Effect of materials and design on the bending stiffness of tennis rackets: https://doi.org/10.1088/1361-6404/ac1146. Review of auxetic materials for sports applications: Expanding options in comfort and protection: https://doi.org/10.3390/app8060941.
This case study is about the application of auxetic materials to sports equipment. Particularly, it is about the development of the first ever tennis racket to feature auxetic fibre-polymer composites [1]. In our work, we aim to combine the exciting fields of sport and advanced materials to engage people with science, technology, engineering, and maths (STEM). Indeed, our work is multi-disciplinary. Dr Mohr is the R&D Manager for PreDevelopement at HEAD and brings expertise in tennis racket engineering, Dr Allen and Professor Alderson are academics and bring respective expertise in sports engineering and smart materials.
Dr Allen has been researching the mechanics of sports equipment for many years, with a focus on tennis rackets [2]. One project involved characterising the properties of over 500 diverse rackets dating back to the origins of the game in the 1870s to the present day. The rackets were from various collections, including the Wimbledon Lawn Tennis Museum in London, and HEAD in Kennelbach Austria, where Dr Mohr works. The museum houses particularly old and rare rackets, whereas the collection at HEAD has a broad range of more modern designs. Initial work involved developing techniques for efficiently characterising many rackets [3]. Subsequent publications describe how a shift in construction materials – from wood to fibre-polymer composites – around the 1970s and 1980s led to lighter and stiffer rackets, with shorter handles and larger heads [4], [5]. Indeed, the application of new materials has driven the development of tennis rackets, and further advances are likely to come from developments in materials and manufacturing techniques.
Professor Alderson has been researching smart materials and structures for many years, with a focus on auxetic materials [6]. Auxetic materials have a negative Poisson’s ratio, which means that they fatten when stretched and become thinner when compressed. A negative Poisson’s ratio can enhance other properties, including vibration damping. Dr Allen and Professor Alderson have been working together to apply auxetic materials to sports equipment [7]. Dr Allen discussed this work on auxetic materials with Dr Mohr, and this led to the collaboration between the three parties that resulted in the new racket design [1].
Auxetic fibre-polymer composites were particularly appealing to Dr Mohr for application in tennis rackets, as they can be made using conventional fibres and resins, by simply arranging the fibres in specific orientations [8]. Following a visit to HEAD, where he was able to see the prototyping facilities, Professor Alderson developed various auxetic fibre-polymer composites, using the materials already being used by HEAD to make rackets. HEAD then developed prototype rackets incorporating these auxetic fibre-polymer composites at their research and development facility in Kennelbach. The racket designs were further developed and refined through testing, both in the laboratory and on the tennis court with players providing feedback.
The first tennis racket with auxetic fibre composites was released in late 2021, in the form of the HEAD Prestige (Figure 1a). The Prestige was followed by the release of a new racket silo (collection) in early 2022 in the form of the Boom (Figure 1b). Drs Mohr and Allen and Professor Alderson are now exploring options for further applying auxetic materials to tennis rackets. Dr Allen’s teaching case study on the historical development of the tennis racket [4] has been enriched by including the story behind the development of the new auxetic fibre-polymer composite rackets [1]. He also includes discussion of emerging topics in the case study that could be applied to tennis rackets, such as more automated manufacturing techniques like additive manufacturing, and more environmentally friendly materials, like natural fibres and resins [5]. We hope that the new tennis rackets will raise awareness of auxetic materials amongst the public, and the case study will help inspire others to use topics like sports engineering and advanced materials to support their STEM teaching and public engagement.
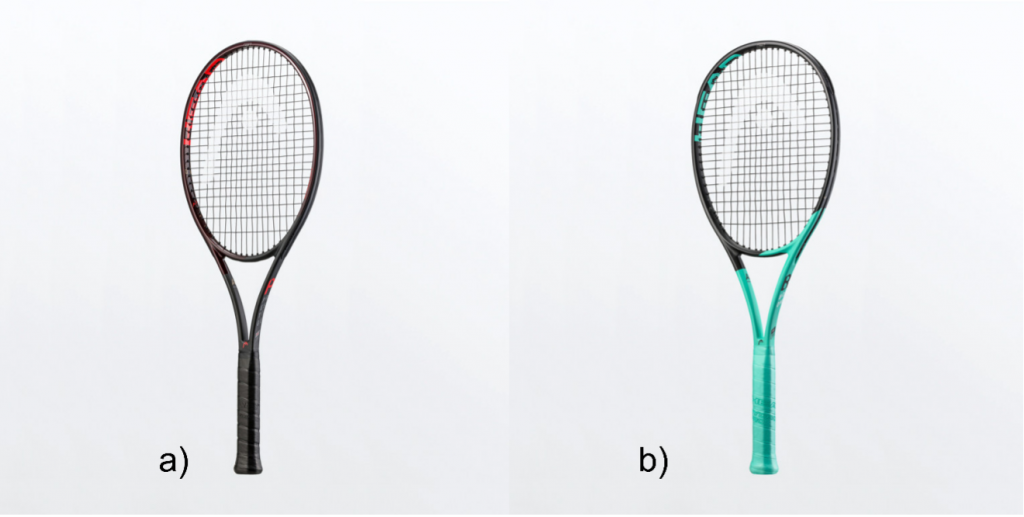
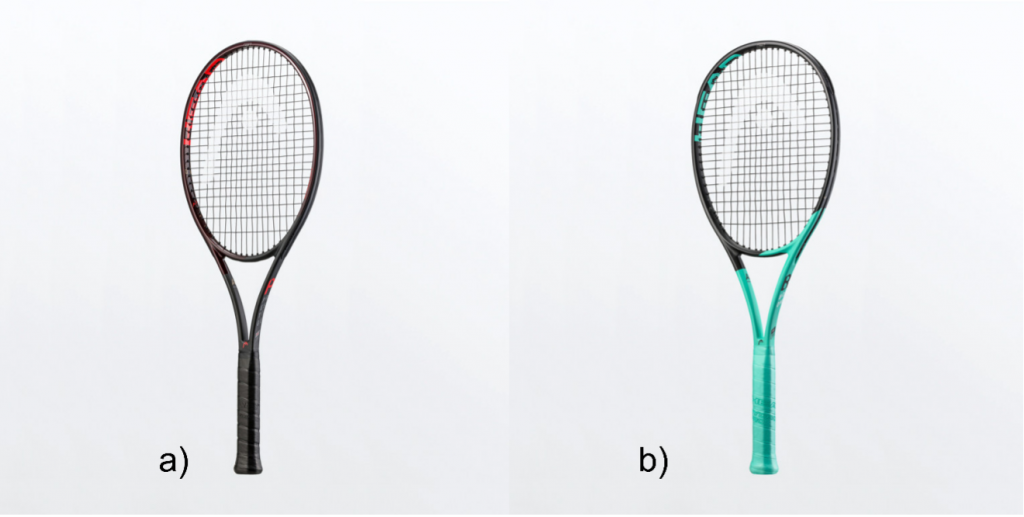
Figure 1 Examples of HEAD rackets featuring auxetic fibre-polymer composites, a) Prestige Pro and b) Boom Prom.
References
[1] HEAD Sports, “Auxetic – The Science Behind the Sensational Feel,” 2021. https://www.head.com/en_GB/tennis/all-about-tennis/auxetic-the-science-behind-the-sensational-feel (accessed Feb. 05, 2022). [2] T. Allen, S. Choppin, and D. Knudson, “A review of tennis racket performance parameters,” Sport. Eng., vol. 19, no. 1, Mar. 2016, doi: 10.1007/s12283-014-0167-x. [3] L. Taraborrelli et al., “Recommendations for estimating the moments of inertia of a tennis racket,” Sport. Eng., vol. 22, no. 1, 2019, doi: 10.1007/s12283-019-0303-8. [4] L. Taraborrelli, S. Choppin, S. Haake, S. Mohr, and T. Allen, “Effect of materials and design on the bending stiffness of tennis rackets,” Eur. J. Phys., vol. 42, no. 6, 2021, doi: 10.1088/1361-6404/ac1146. [5] L. Taraborrelli et al., “Materials Have Driven the Historical Development of the Tennis Racket,” Appl. Sci., vol. 9, no. 20, Oct. 2019, doi: 10.3390/app9204352. [6] K. E. Evans and A. Alderson, “Auxetic materials: Functional materials and structures from lateral thinking!,” Adv. Mater., vol. 12, no. 9, 2000, doi: 10.1002/(SICI)1521-4095(200005)12:9<617::AID-ADMA617>3.0.CO;2-3. [7] O. Duncan et al., “Review of auxetic materials for sports applications: Expanding options in comfort and protection,” Applied Sciences (Switzerland), vol. 8, no. 6. 2018, doi: 10.3390/app8060941. [8] K. L. Alderson, V. R. Simkins, V. L. Coenen, P. J. Davies, A. Alderson, and K. E. Evans, “How to make auxetic fibre reinforced composites,” Phys. Status Solidi Basic Res., vol. 242, no. 3, 2005, doi: 10.1002/pssb.200460371.
Any views, thoughts, and opinions expressed herein are solely that of the author(s) and do not necessarily reflect the views, opinions, policies, or position of the Engineering Professors’ Council or the Toolkit sponsors and supporters.